Solder Bump Vertical Probe Cards Increasing Test Parallelism
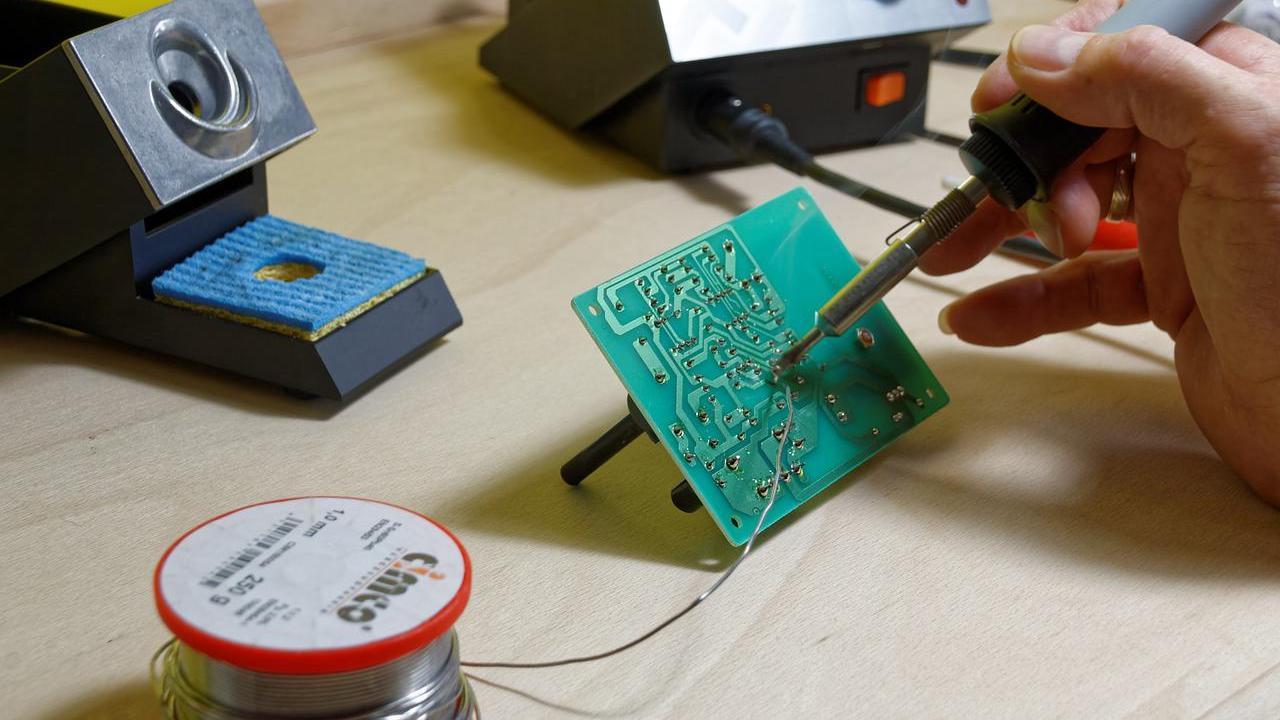
As fine pitch 3D wafer-level packaging becomes more popular in semiconductor industries, wafer-level prebond testing of various interconnect structures has become an important challenge. Formfactor offers a range of MEMS, solder bump vertical probe cards to address these challenges. These cards offer high parallelism, stable contact resistance and superior contact precision for wafer-level probing.
High Parallelism
Increasing test parallelism has become a priority for probe card manufacturers as testing becomes more complex and the number of devices to be tested increases. Several companies report ability to test 8 to 256 dies in parallel, depending on the type of device and probe card capabilities.
One approach is to use built-in self-test circuits on the die, which can fan out test signals and allow multiple probe cards to write test signals to the same set of die contacts on the die. This enables multiple wafers to be tested at the same time without increasing the cost of each probe card.
However, this isn’t always possible. Often, the underlying design of the chip requires that the pads on the wafer be arranged in certain patterns for this to be effective. This causes a problem with needle-type probe cards, as they require that the pads be arranged in a dense array, which makes it difficult to parallel probing multiple dice using this type of card.
Stable Contact Resistance
As the market for flip chip devices grows to accommodate larger numbers of pins with greater electrical performance, testing configurations and levels of parallelism are changing. In addition, new device designs require higher levels of contact resistance to resist the piercing force required for the testing process.
The probing mechanism in conventional solder bump vertical probe cards involves flexural deformation of the horizontal beam in its middle portion. This deformation converts into a resulting vertical displacement of the tip of the probe.
This undesired enlargement of the pitch of the probe leads to poor electrical contact and increased probing forces, which can be a problem during the testing process. The contact pressure applied to the horizontal beam also tends to shear off the substrate on which it is attached.
In addition, oxide accumulation on the probe tips can alter the critical measurement of contact resistance in an unpredictable manner. This accumulation is due to the effect of scrubbing when the probe tip touches the terminal during overdrive. This scrubbing action flattens the top of the terminal and breaks its oxide, which exposes the underlying metal or alloy.
Superior Contact Precision
Solder Bump Vertical Probe Cards deliver superior contact precision to the device under test (DUT) and its supporting IC test system. This is particularly beneficial when testing ICs with multiple solder bump bond pads and/or in multi-DUT test environments.
Typically, the device under test is supported on a chuck. This chuck is bolted to the upper side of a membrane probing assembly (such as a support element) that is in turn bolted to the probe head.
The probe head is positioned on the wafer, and the membrane assembly has a series of radially extending arm segments arranged in a pattern that enables pressing engagement with each of the contacts on the device under test. The membrane assembly also extends in an inclined manner along the angled sides of these radially extending arm segments so as to clear any upright components that may surround the pads on the device under test.
These membrane probing assemblies are especially useful in IC production testing at temperatures higher than ambient because they offer the ability to provide a reliable electrical connection between each of the contacts on the device under test and its respective pad. This ensures that the contacts on the devices under test are not subjected to inductive cross-talk that could otherwise cause functional failures.
Low Contact Force
Sensitive devices-including flip chip die and those using low-k dielectrics-are prone to damage during testing by applying too much contact force. Therefore, probe card manufacturers have focused on developing a variety of strategies to reduce contact force. Some of these include improved planarity, changes in the shape of the probe tip to distribute forces over a larger area, and new materials.
Another key component of a successful probe design is the lateral scrub motion achieved by the probe arm. This motion removes oxide and other impediments to reliable electrical contact.
In one exemplary embodiment, a vertically folded probe arm is employed to achieve a total height of about 0.8 mm (i.e., well within micro-fabrication height limitations). This enables the application of substantial lateral scrub motion to the probe tip which may be sufficient to effectively remove oxide and other impediments to reliable contact.
Laterally driven probing can be advantageous in a variety of applications with circuits adversely affected by insulating residue or oxide film. This can result in a significant increase in the yield of an IC, as well as minimize test time and costs.
We are excited to announce the **launch of the Sharkbow Marketplace!** 🎉 Now you can:
- 🛍️ List and sell your products – Open your own store easily.
- 📦 Manage orders effortlessly – Track sales and communicate with buyers.
- 🚀 Reach thousands of buyers – Expand your business with ease.
Start selling today and grow your online business on Sharkbow! 🛒
Open Your Store 🚀 ✖🚀 What Can You Do on Sharkbow?
Sharkbow.com gives you endless possibilities! Explore these powerful features and start creating today:
- 📝 Create Posts – Share your thoughts with the world.
- 🎬 Create Reels – Short videos that capture big moments.
- 📺 Create Watch Videos – Upload long-form content for your audience.
- 📝 Write Blogs – Share stories, insights, and experiences.
- 🛍️ Sell Products – Launch and manage your online store.
- 📣 Create Pages – Build your brand, business, or project.
- 🎉 Create Events – Plan and promote your upcoming events.
- 👥 Create Groups – Connect and build communities.
- ⏳ Create Stories – Share 24-hour disappearing updates.
Join Sharkbow today and make the most out of these features! 🚀
Start Creating Now 🚀- Art
- Causes
- Crafts
- Dance
- Drinks
- Film
- Fitness
- Food
- Jocuri
- Gardening
- Health
- Home
- Literature
- Music
- Networking
- Alte
- Party
- Religion
- Shopping
- Sports
- Theater
- Wellness